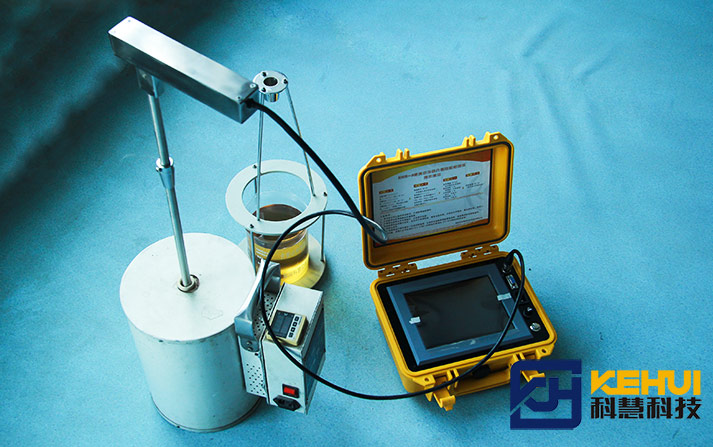
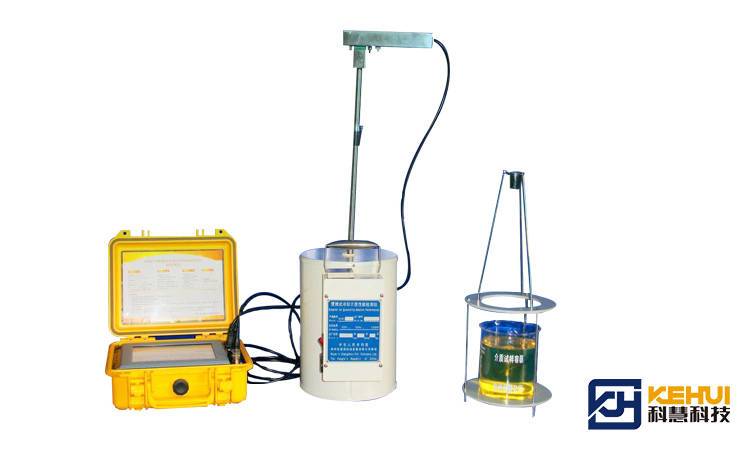
Main functions and uses:1. Temperature control
The quenchometer can accurately control the heating and cooling temperatures. During the heating process, the quenchometer ensures that the metal material reaches and maintains the required temperature to achieve the required metallographic structure transformation.
2. Cooling rate control
The cooling rate is an important factor affecting the quenching effect. The quenchometer can adjust the flow and temperature of the cooling medium (such as water, oil, air, etc.) to ensure that the material is cooled at an appropriate rate to avoid material defects caused by overcooling or overheating.
3. Time control
The heating and cooling times during the quenching process need to be strictly controlled. The quenching instrument can set and monitor the duration of heating and cooling to ensure that each stage meets the process requirements.
4. Data recording and monitoring
The quenching instrument is equipped with data recording and monitoring functions, which can record parameters such as temperature, time and cooling rate in real time. These data help to analyze and optimize the quenching process and improve the consistency and quality of the product.
5. Automated operation
Modern quenching instruments usually have an automated control system that can automatically perform the quenching process according to preset process parameters, reduce manual intervention, and improve production efficiency and precision.
6. Quality control
By precisely controlling the various parameters of the quenching process, the quenching instrument can ensure the consistent quality of each batch of products, meet specific hardness, strength and toughness requirements, and reduce scrap rates.
Application scenarios:Quenching instruments are widely used in many industries. The following are some typical application scenarios:
Mechanical manufacturing: quenching treatment of parts such as gears, shafts, springs and bolts to improve their hardness and wear resistance.
Automotive industry: quenching treatment of key components of engine components, transmission system parts, braking systems and suspension systems.
Aerospace: Quenching treatment of aircraft structural parts and engine components to improve their strength and heat resistance.
Tool manufacturing: Quenching treatment of industrial tools such as cutting tools, molds, and drills to improve their hardness and service life.
Iron and steel industry: Quenching process in steel and alloy production to optimize the microstructure and mechanical properties of materials.
Energy industry: Quenching treatment of key components such as wind power generation equipment, nuclear power equipment, and oil drilling equipment.
Military manufacturing: Quenching treatment of key components of weapons and military vehicles.
Mold manufacturing: Quenching treatment of mold steel to improve its hardness and wear resistance.
Electronics industry: Quenching treatment of precision parts and connectors to enhance their strength and durability.
Medical devices: In the manufacturing process of medical devices, quenching treatment is used to improve the safety and durability of the devices.