What is Orbital Welding?
Orbital welding is the automatic or mechanized welding of tubes or pipe in-place with an electrode rotating (or orbiting) 360 degrees around the workpiece. Orbital welding can be conducted on tube or pipe with the addition of filler material or as a fusion process. Its creation has been vital to the ever-growing standards and success of many industries.
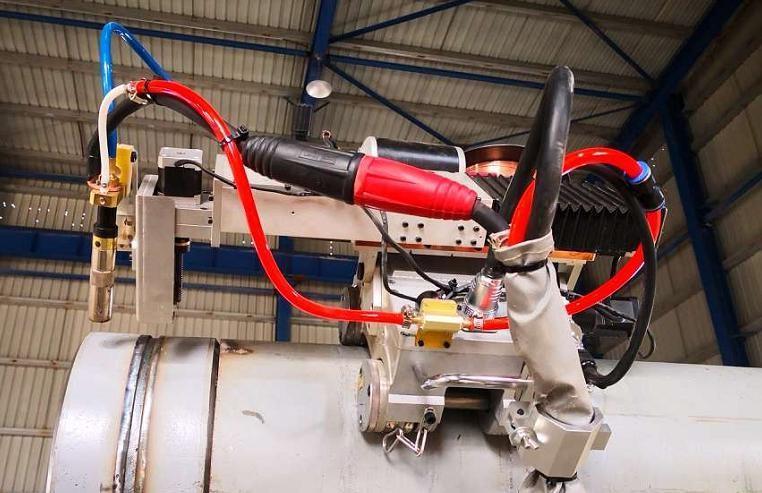
Benefits of Orbital Welding
Manual welding can be unreliable, and workloads can often become greater than even the most skilled welders can handle. With an orbital welding system, uniform welds can be created quickly with a minimized risk of human error.
The orbital welding process is designed to produce welds that meet ASME BPE acceptance criteria. Consistent bead size and full penetration create smooth surfaces that prevent microbiological growth and possible contamination of the product. This is especially beneficial in critical applications such as in the pharmaceutical or food & beverage industries.
Orbital Welding Benefits:
Increased Speed and Process Efficiency
Weld Quality - Accuracy and Consistency
Weld Repeatability
Weld Cleanliness
Versatility for Unique Applications (piece unable to be rotated, has poor visibility, or is in a hard to reach place)
Orbital Welding Prevents:
Poor Penetration
Lack of Fusion
Poor Purging Techniques
Orbital Welding Applications and Industries
Applications
Sanitary Tubing
Tube to Tube
Tube to Fitting
Fitting to Fitting
Pipe
Pipe to Pipe
Pipe to Fitting
Exotic Alloy Application
Tube to Tube Sheet
Overlay Applications
Industries
Semiconductor
Biotechnology
Pharmaceutical
Cosmetic
Food & Dairy Processing
Breweries & Wineries
Electronics
Chemical
Aerospace
Nuclear Piping
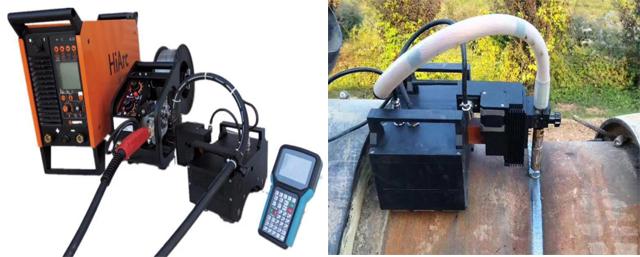
Orbital Welding Equipment
An orbital welding system is composed of three pieces: the power supply, water cooler, and the weld head.
Power Supply
The power supply, also known as a power source or controller, is where weld programming is conducted. It communicates weld speed, amperage, purging time and more to the weld head. The power supply also documents welds, stores programs for future use and features a printer for documentation purposes after each weld.
Water Cooler
The water cooler is an important component to the orbital welding system. It interconnects to the weld head and holds cooling fluid. We recommend a low conductivity coolant/antifreeze jug of glycol. Utilizing a pump, the water cooler flows the coolant through the weld head coolant lines and into the weld head. This allows the weld head to run at 100% duty cycle and not to overheat the inner components of the weld head during the weld.
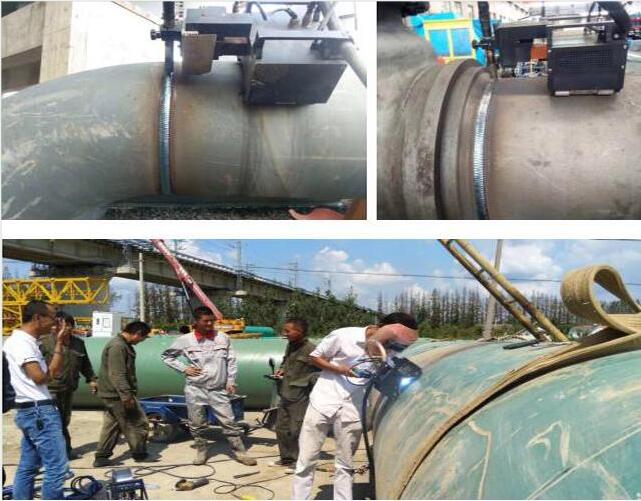
Orbital Weld Head
Weld heads connect to the power supply and water cooler through a series of cable connections. There are two options when it comes to weld heads: enclosed heads and open weld heads.
Enclosed Weld Heads
Enclosed weld heads are often referred to as closed or fusion weld heads. They are closed, as the name suggests, creating an inert atmosphere chamber that surrounds the weld joint. This encapsulated environment helps to create fusion welds with a decreased risk for blemishes or other imperfections.
No welding helmet is needed while conducting a weld. Internally, the weld head rotor holds the tungsten electrode in place as it orbits around the tube or pipe, creating a fusion weld. This type of weld head is typically used for orbital tube welding but can be used on thin-walled pipe.
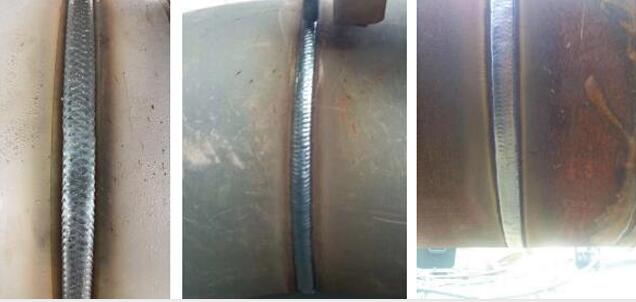
Open Weld Heads
These weld heads are most often utilized for pipe welding applications where filler wire is required, and multiple passes are required to complete the weld. There are two styles of weld head offered in the open face design for pipe welding. The clamping style head uses a vise clamping system to mount to the workpiece. The low profile or guide ring style uses a tracking system that mounts to the workpiece and attaches to the track.
Contact Kehui to find out if an orbital welding machine is right for your application.