Automated filling machines usually achieve fully automatic filling through five steps: raw material supply, transportation and processing, filling, sealing, and packaging. Currently, they have been widely used in food, beverage, chemical, new energy, pharmaceutical and other industries. This article will explain in detail the operation process of automated filling machines.
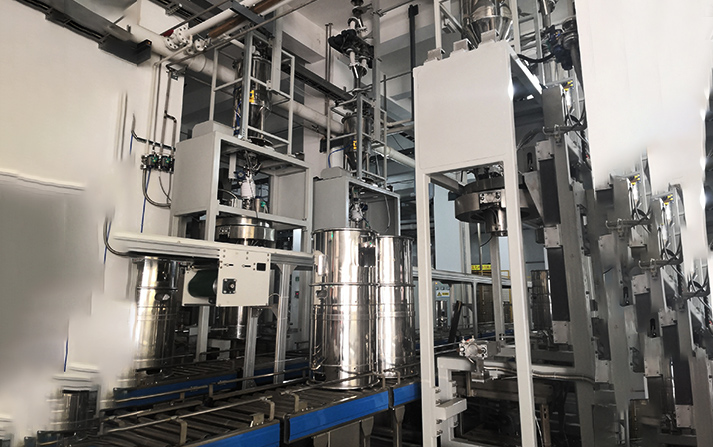
Raw material supply and storage:
Raw materials are usually stored in storage tanks in the form of liquid or powder. These storage tanks can be of different sizes and types, selected according to production needs.
Automated filling machines need to ensure adequate supply of raw material storage tanks, and the raw material levels in the storage tanks can be monitored through automated control systems.
Conveying and Handling:
The conveyor system is responsible for transporting raw materials from storage tanks to filling equipment. This involves conveying pipes, pumps and other equipment to ensure that raw materials can flow smoothly from the storage tank to the filling equipment.
During the transportation process, the raw materials may need to be processed, such as filtration, heating, cooling, etc., to ensure the quality and suitability of the raw materials.
Filling stage:
Automatic filling machines are the core part of
automated filling lines. They are responsible for accurately injecting raw materials from storage tanks into packaging containers. Filling machines typically operate according to preset parameters and have a high degree of automation and precision.
During the filling process, different types of packaging containers and different filling volume requirements may need to be considered.
Sealing and packaging:
Once the raw material filling is completed, sealing operations may be required to ensure the sealing and safety of the product. The sealing machine is usually integrated with the filling machine to automatically complete the sealing process.
Sealed products may need further packaging, and appropriate packaging methods and equipment should be selected based on the characteristics and needs of the product.
Quality inspection and inspection:
Automated filling production lines are usually equipped with quality inspection systems to check the appearance, sealing, packaging, etc. of the product to ensure that the product meets quality standards.
Quality inspection systems may include visual inspection systems, weight inspection systems, etc., which can quickly and accurately detect product quality, and record and report.
Data recording and tracing:
Automated production lines collect various data, such as production rate, filling volume, quality inspection results, etc., to monitor and optimize the production process.
The traceability system can track the production process and raw material sources of each product to ensure product quality and safety and meet regulatory requirements.
So far, automated filling production lines have been widely used in food, beverage, chemical, new energy, pharmaceutical and other industries. The product types involved include beverages, juices, chemicals, pharmaceutical raw materials, detergents, etc. These production lines can improve production efficiency, ensure product quality, reduce labor costs, and help meet growing market demand.