Welding is a vital process, and
Orbital welding machine, as one of the representatives of modern automated welding technology, is widely used in pipeline installation projects in various fields such as oil, natural gas, chemical industry, water supply, and heating. This article will explain to you today the working principle of the orbital welding machine and its application in pipeline engineering.
The working principle of the Orbital welding machine is based on orbital
automated welding technology. It mainly includes the following steps:
1. Set welding parameters: The operator sets the welding parameters according to the welding requirements, including current, voltage, welding speed, etc.
2. Clamping the workpiece: The workpiece is clamped in the fixture of the orbital welding machine to ensure the stability and positional accuracy of the workpiece.
3. Start welding: After the welding machine is started, the
welding head begins to move along the track of the workpiece while performing automated welding operations.
4. Automatic control: During the welding process, the orbital welding machine automatically adjusts the welding current and voltage according to the preset welding parameters to ensure the stability of the welding process and the quality of the weld.
5. Complete welding: When the welding is completed, the orbital welding machine stops moving and the welding head returns to the initial position to complete the entire welding process.
Application of orbital welding machine in pipeline engineering
Application of orbital welding machine:
Orbital welding machines are widely used in pipeline engineering, covering various fields such as petroleum, natural gas, chemical industry, water supply, and heating. Its main application scenarios include but are not limited to:
1. Pipe installation and connection: During the pipeline installation process, the orbital welding machine can achieve efficient connection of the pipeline, ensure the quality of the weld, and ensure the sealing and stability of the pipeline.
2. Pipeline maintenance and repair: For aging or damaged pipelines, orbital welding machines can perform precise welding repairs, extend the service life of the pipeline, and reduce maintenance costs.
3. Pipe processing and manufacturing: During the pipeline processing and manufacturing process, the orbital welding machine can realize automated welding of pipelines, improve production efficiency, and ensure product quality.
Advantages of orbital welding machines:
Orbital welding machines have many advantages over traditional manual welding, which are mainly reflected in the following aspects:
1. High-precision welding: The orbital welding machine adopts an automated control system, which can achieve high-precision welding and ensure the quality and consistency of the weld.
2. High-efficiency production: The orbital welding machine adopts an automated production process, which can achieve continuous and efficient welding operations and improve production efficiency.
3. Save labor costs: The automated operation of the orbital welding machine reduces dependence on labor, saves labor costs, and reduces production costs.
4. Wide applicability: The orbital welding machine is suitable for welding various pipe materials and diameters, including carbon steel, stainless steel, alloy steel, etc. Whether it is a small diameter pipe or a large diameter pipe, welding needs can be met.
5. Environmentally friendly: The orbital welding machine produces less waste gas during the welding process, reducing environmental pollution and meeting environmental protection requirements.
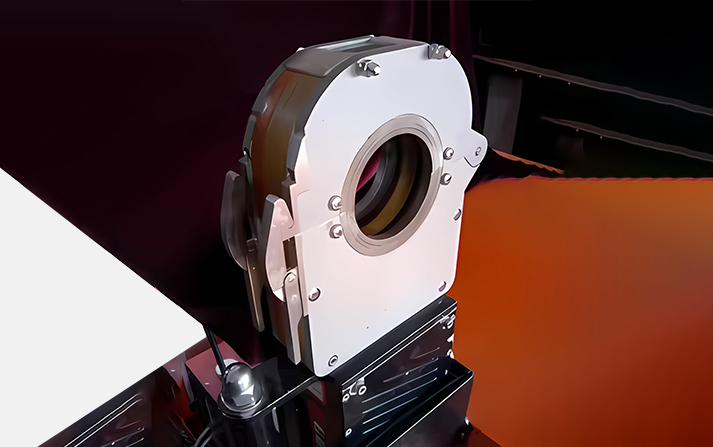
In summary, the application of orbital welding machines in pipeline engineering provides efficient and accurate welding solutions for pipeline manufacturing and installation, and promotes the development and progress of the pipeline engineering industry.