Shielded Metal Arc Welding (SMAW), also known as stick, is generally the default welding process for pipe. However, in spite of its wide use, SMAW is probably not the best way to weld pipe. It is merely the welding process that has been used to weld pipe the longest.
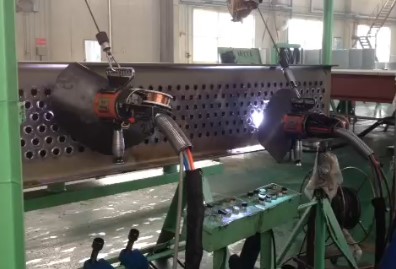
Since the development of SMAW, several other arc welding processes have emerged and gained widespread use. Wire feed arc welding processes like Gas Metal Arc Welding (GMAW) and Flux Core Arc Welding (FCAW) are significantly easier to perform than traditional stick welding. Gas Tungsten Arc Welding (GTAW) requires a great deal of skill to use, but produces welds last longer and resist corrosives and high pressure better than welds made using other processes.
Which Welding Process Creates the Best Welds?
Which welding process offers the best welds depends on what qualities of the welding process are considered most critical for a given project. For instance, if speed matters most, a project manager might consider FCAW to be the best. The principles involved in FCAW are essentially the same as SMAW, but in FCAW the flux is provided by the core of the wire electrode. Due to the use of a continuously fed wire electrode, the process is quick, and thanks to the flux, it’s also easy to use and forgiving of less-than-perfect surrounding environments. However, the welds that it produces are not perfect. For a higher quality weld, it’s necessary to choose a welding process that uses gas shielding.
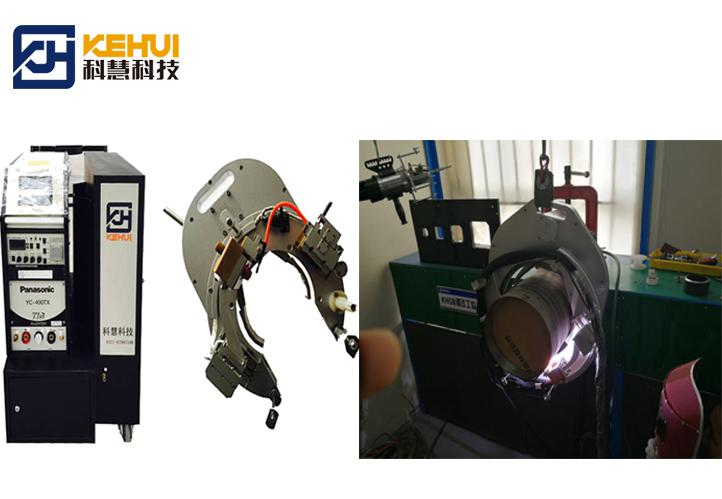
GMAW and GTAW arc welding both use inert gas to shield the weld during the welding process. While the use of shielding gas means that the process isn’t ideal for fieldwork—wind can easily blow the gas away—the quality of the welds produced using these processes has led to some projects using special barriers or even erecting full structures to enable the use of gas-shielded welding processes. While GMAW beats GTAW in terms of speed, GTAW Welding provides the Most Consistent, Clean, and Reliable Welds.
Unfortunately, the manual GTAW welding process has several disadvantages. It is difficult to master and it takes a great deal of training and experience before a welder can correctly weld GTAW. It is also a very slow process. As a result, manually performing deep groove or narrow groove pipe welds takes a prohibitive amount of time. Usually, if manual GTAW is used weld pipe, it is only used for the root pass—the part of the weld in actual contact with the pressurized or corrosive material in the pipe—while the rest of the groove is filled in using FCAW, GMAW, or even SMAW processes. However, developments in automation have solved many of the disadvantages of GTAW by making it possible to perform reliable GTAW welds using orbital welding.

Why Automated Orbital Welding Is the Best Way to Weld Pipe
Orbital welding is a mechanized welding process that allows the welder to program the weld controller with the weld parameters, such as the feed rate of filler material, travel speed, weld current, arc voltage, and other variables. By automating the weld procedure, orbital welding makes the process easier for the operator and provides a solution to the problem of finding qualified GTAW welders.
Automated orbital welders can be continuously wire-fed as well as autogenous. Wire feeds significantly speed up the orbital GTAW welding process for narrow groove welds and other weld types that require a great deal of filler material. Automated welding can improve welding productivity for both thick-walled pipe and pipe welding where no filler is required. Orbital machines produce high-quality welds more easily and efficiently than manual GTAW, making automated orbital welding the best way to weld pipe.
kehui welcomes the opportunity to discuss your specific needs.