Welding in the overhead position—with the workpiece directly above the welder—is widely thought to be the most difficult welding position. Pipe welding is also well known to be particularly challenging welding work. The truth is that welding pipe is difficult because it involves every welding position—including overhead—and the welder must be able to weld in all of these positions with equal facility, repeatedly, to make a single satisfactory weld.
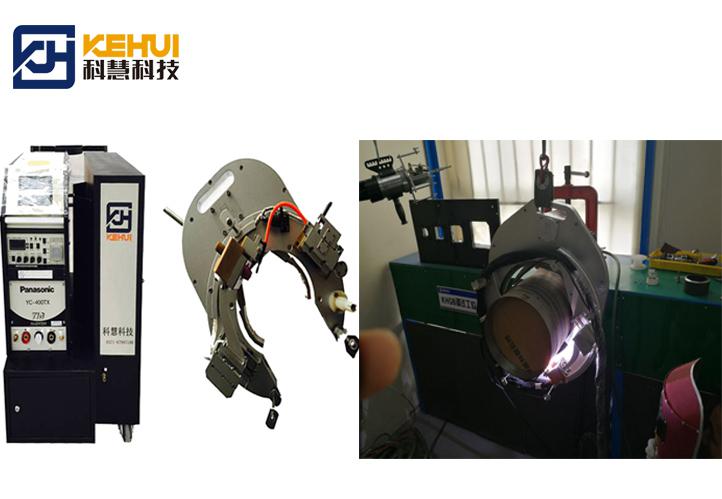
The Challenges of Overhead WeldingManual pipe welding involves moving through every position of welding.
Overhead welding is probably the most disliked manual welding position. Trying to work with one’s hands above the head (and in some cases while laying on your back) isn’t easy in the best of circumstances. Doing so while it rains red hot metal requires determination. The welder must fight the force of gravity unfailingly through fatigue and burns in order to produce a quality weld that will hold up to both internal pressure and external forces—and must maintain this consistency through several passes to complete a joint.
Pipe welding, as well, has its own challenges. The shape of a pipe means the welder must change angles and position as they work around the circumference of a pipe, and at least two of those positions require overhead welding.
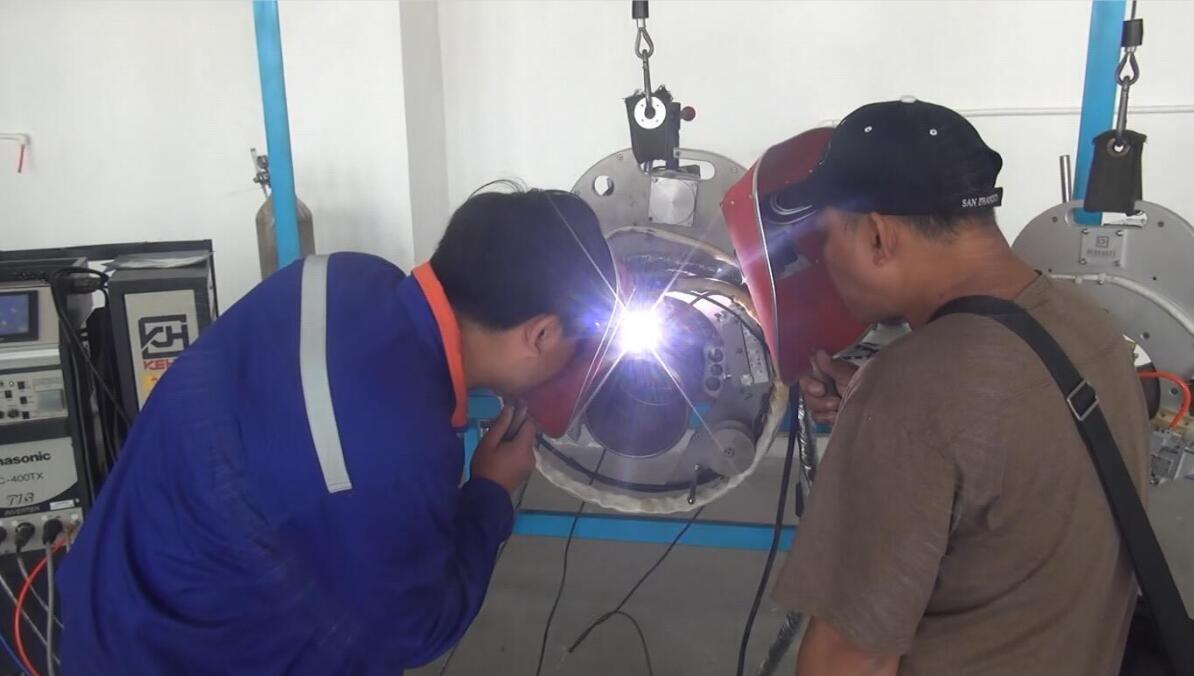
The Unique Challenges of Manual Pipe WeldingManually welding pipe requires the use of every welding position in order to create a consistent weld around the full circumference of the pipe. The welder divides the pipe’s circumference into quarters, and welds one quarter at a time, stopping between each quarter to reposition themselves.
Transitioning between positions during the weld makes maintaining the correct pattern, angle, and travel speed more difficult. When a welder chooses a new position, they try to find one that allows them a wide range of motion while enabling them to brace themselves so that they aren’t forced to hold steady purely through muscle tension.
The type of location where piping is most often installed adds another wrinkle to the tricky process of manual pipe welding. Pipes tend to be located either close to the ground or near the ceiling. Overhead pipe welding often involves arc welding in a tight, awkward space below the pipe or standing on a ladder reaching up. This makes the transition between vertical and overhead pipe welding positions even more difficult to manage. Fortunately, automated orbital welding successfully eliminates all of these challenges posed by welding pipe in the overhead position.
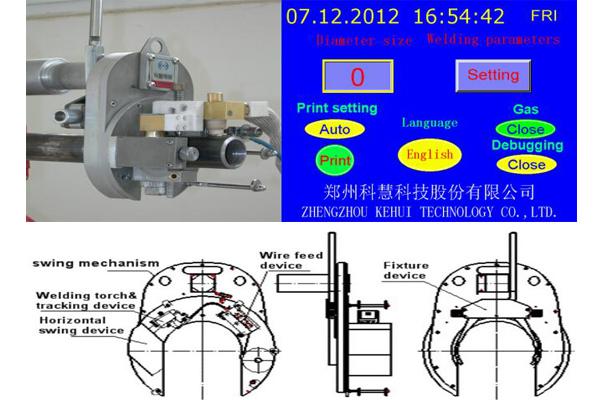
How Orbital Welding Simplifies Overhead Pipe WeldingOrbital welding makes pipe welding, especially narrow groove welding, easier.
One of the most obvious benefits that mechanized welding processes offer is to remove the welder from the fall line of the molten metal. Even semi-automated orbital welding, in which the welder operates a weld head using a remote pendant, allows the welder far more leeway in choosing their position than manual welding does.
Orbital pipe welding also removes the many opportunities for flaws to form in the weld. Sectioning a weld into quarters means starting and stopping, and each start and stop is an opportunity for foreign materials to enter the weld. If the welder makes a mistake when striking an arc, for example, this could disrupt the shielding gas and include contaminants into the weld. In fact, the more times an arc must be struck, the more likely an inclusion is, and when a pipe weld that requires multiple passes is quartered, the arc needs to be struck many times.
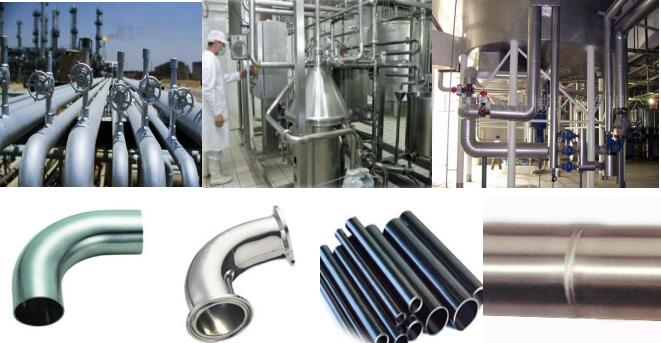
Orbital welding, by comparison, can make each pass in a continuous circuit around the full circumference of the pipe, removing many of the opportunities for contaminants to enter the weld. Since orbital welding weld heads either clamp around a pipe or mount to it using a guide ring, the torch maintains a consistent travel speed and distance from the weld around the entire pipe.
Automated orbital welding simply puts many of the most challenging parts of the pipe welding process under the guidance of a programmed welding controller. This can be especially helpful in the case of overhead pipe welding, where the need to reach, position for, and maintain consistency throughout all welding positions requires not just skill, but also endurance. Using automated orbital welding to weld pipe overhead also makes it possible to efficiently and precisely weld pipe located in difficult or almost inaccessible positions, such as far overhead or close to the ground. Automated orbital pipe welding is the best way to consistently and reliably produce quality pipe welds in any position.