Heat exchanger is a device widely used in industrial fields, mainly used to transfer heat between fluids of different temperatures. The
tube to tube sheet joint is a crucial component in the heat exchanger, and its design and manufacturing quality directly affect the performance and service life of the heat exchanger.
Structure And Function Of Tube To Tubesheet Joints
The
tube to tube sheet joint is located between the tube bundle and the tube sheet of the heat exchanger and plays a role in fixing and sealing. Heat exchangers usually consist of multiple parallel tubes that are fixed to a tube sheet at one or both ends. The tube sheet not only has to withstand the pressure difference between the inside and outside of the tube, but also ensures that the fluid does not leak and ensures effective heat transfer.
Manufacturing Process Of Pipe And Tube Sheet Joints
There are three main ways to connect pipes and tube-sheet joints: welding, expansion joints and weld-expansion composite joints:
1. Welding:
Tube to tubesheet welding is a common connection method, especially suitable for high temperature and high pressure conditions. When welding, the pipe and tube sheet are firmly connected by melting the metal material. The advantage of this method is high joint strength and good durability, but it requires a high level of technology and strict quality control. Usually companies will purchase automatic tube-to-tube-sheet welding machines to operate the welding to avoid welding defects such as cracks and imperfections. Weld through.
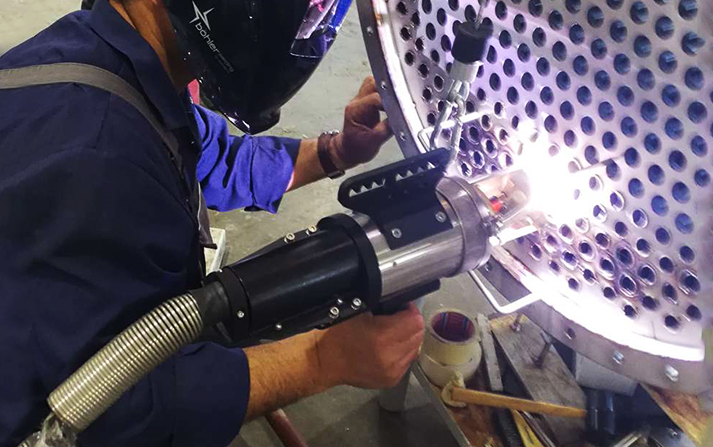
2. Expansion joint: Expansion joint uses special tools to mechanically expand the pipe in the tube plate hole to make it fit tightly. This method is simple and quick, suitable for medium and low voltage situations. The advantage of expansion joints is that the process is relatively simple and the cost is low, but the quality of expansion joints is greatly affected by the materials of pipes and tube sheets and the operating process.
3. Weld expansion composite joint: This method combines the advantages of welding and expansion joints. The expansion joint is first performed, and then welded on the contact surface to increase the sealing and strength of the joint, and is suitable for demanding working conditions. Weld expansion composite joints can ensure good mechanical strength and prevent leakage, and are widely used in high-pressure heat exchangers.
Factors Affecting Joint Performance
The performance of pipe-to-tubesheet joints is affected by many factors, including material selection, processing technology, operator skill level, and usage environment.
1. Material selection: Joint materials must have good corrosion resistance, mechanical strength and processability. Commonly used materials include stainless steel, copper and their alloys.
2. Processing technology: Different connection methods have different process requirements. For example, welding requires high-precision welding equipment and process parameter control, while expansion joints require precise expansion tools and reasonable expansion parameters.
3. Operating technology: The technical level of the operator directly affects the quality of the joint. Skilled welding and expansion joint technology can effectively reduce defects and improve joint reliability.
4. Usage environment: The working conditions in which the joint is located, such as temperature, pressure, medium corrosivity, etc., will affect its performance. These factors need to be fully considered during design and appropriate joint types and materials should be selected.
Inspection And Maintenance Of Pipe And Tube Sheet Joints
To ensure the reliability and service life of pipe-to-tubesheet joints, regular inspection and maintenance are required. Common testing methods include non-destructive testing (such as ultrasonic testing, X-ray testing), pressure testing, etc. Through inspection, potential defects and problems can be discovered in time, and corresponding maintenance measures can be taken, such as replacing pipes and repairing welds, etc.
In Conclusion
Tube-to-tubesheet joints play a key role in heat exchangers, and their design and manufacturing quality are directly related to the overall performance and safety of the equipment. Through reasonable material selection, precise processing technology, strict quality control, and regular testing and maintenance, the reliability of the tube and tube sheet joints can be effectively improved, the service life of the heat exchanger can be extended, and the smooth progress of industrial production can be ensured.